新闻中心
导轨丝杠的原装配步骤及装配工艺问题
来源:http://www.jngongrun.com/ 日期:2023-03-21 发布人:
先装好直线导轨,以直线导轨的滑座为基准校正丝杠,再以丝杠两端支承座安装孔配作固定螺纹孔。用螺钉固定丝杠后,用磁力表座将千分表固定在直线导轨滑座上,测量丝杠、侧母线和丝杠径向跳动量,保证丝杠的平行度及跳动量在要求范围内。
Install the linear guide rail first, calibrate the lead screw based on the sliding seat of the linear guide rail, and then match the mounting holes of the support seats at both ends of the lead screw as fixed threaded holes. After fixing the lead screw with a screw, use a magnetic meter holder to fix the dial indicator on the linear guide rail slide. Measure the radial runout of the lead screw, side bus, and lead screw to ensure that the parallelism and runout of the lead screw are within the required range.
重新配作支承座定位锥销,装好锥销后再复检一次。装配各步骤采用的处理方法基本正确,检测基准与工艺基准也相符,检测量具精度也能满足要求,被测要素也正确。整个装配过程没有问题,但通过在现场观察,发现装配工艺中仍存在以下问题:
Reassemble the bearing seat positioning taper pin, and recheck it after installing the taper pin. The processing methods used in each step of assembly are basically correct, the inspection benchmark is also consistent with the process benchmark, the accuracy of the inspection measuring tool can also meet the requirements, and the measured elements are also correct. There were no problems during the entire assembly process, but through on-site observation, it was found that the following problems still exist in the assembly process:
(1)使用手电钻铰孔时,由于铰削余量较大,振动较厉害,双手控制不稳,铰刀摆动过大,造成锥孔铰削后上大下小,锥度不是要求的1∶50。用涂色法进行检查,发现锥销与锥孔的接触部位不正确,位置靠近小头一端,不能保证良好的接触精度,受到交变应力与振动时容易松动,从而导致定位精度下降。
(1) When using a hand electric drill to ream holes, due to large reaming allowance, severe vibration, unstable control of both hands, and excessive swing of the reamer, the taper of the tapered hole is not the required 1:50 after reaming. Using the color coating method for inspection, it was found that the contact position between the taper pin and the taper hole was incorrect, and the position was close to the small end, which could not ensure good contact accuracy. When subjected to alternating stress and vibration, it was easy to loosen, resulting in a decrease in positioning accuracy.
(2)机铰后没有留精铰余量,也没有进行手工精铰。圆锥销的配合都是依靠配合面的过盈产生摩擦力来定位的。由于机铰后表面粗糙使实际过盈量减少,造成摩擦力不够,自锁性能下降,当受到交变应力与振动时容易松脱,从而导致定位精度下降。
(2) After machine reaming, there was no allowance for fine reaming, nor was manual fine reaming performed. The fitting of tapered pins is positioned by friction generated by interference on the mating surface. Due to the roughness of the surface after reaming, the actual interference amount decreases, resulting in insufficient friction, reduced self-locking performance, and easy loosening when subjected to alternating stress and vibration, resulting in reduced positioning accuracy.
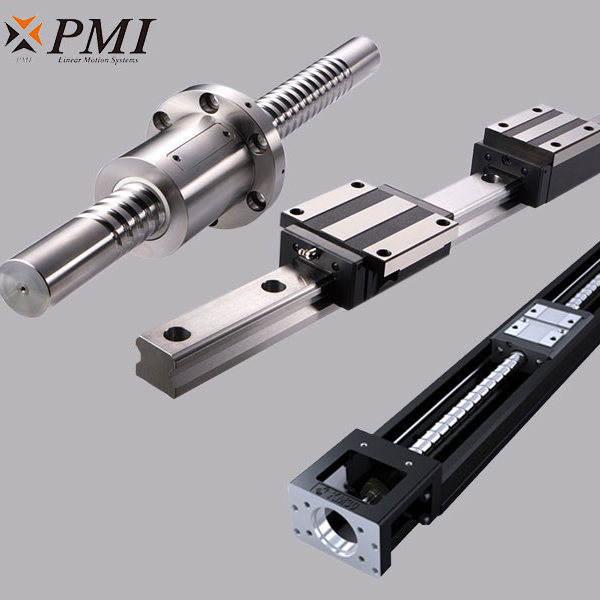
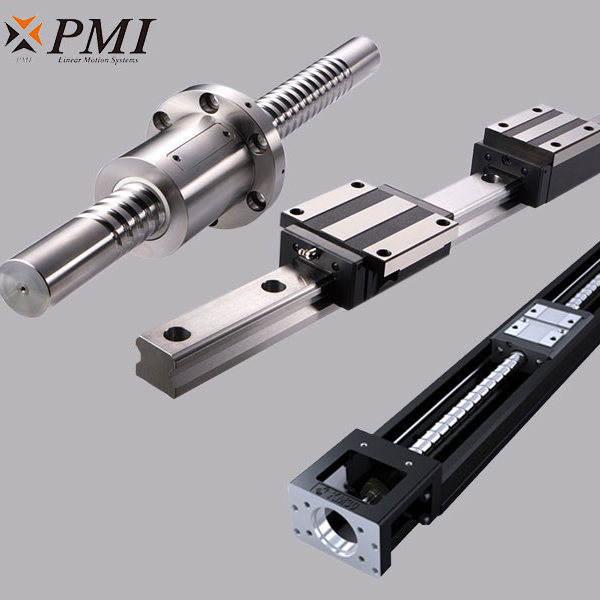
(3)铰孔时孔径控制不严,铰削过程中没用锥销试配,装配时用铜棒轻轻敲入即可。由于不能保证足够的过盈量,装配后的摩擦力过小;受负荷及振动时易造成锥销松动,失去定位作用,导致工作台运动精度差。
(3) The hole diameter was not strictly controlled during reaming, and the taper pin was not used for trial fitting during the reaming process. During assembly, gently tap in with a copper rod. Due to insufficient interference, the friction force after assembly is too small; When subjected to load and vibration, it is easy to cause the taper pin to loosen and lose its positioning function, resulting in poor movement accuracy of the workbench.
(4)在钻孔铰孔等过程中,没有进行防尘处理。虽然丝杠副带有防尘圈,但铸铁粉尘非常细小,且易粘附在丝杠表面。如有少量进入丝杠副传动面,粉尘的研磨作用会加剧丝杠副的磨损,导致丝杠精度下降,降低使用寿命。
(4) During the process of drilling and reaming, no dust prevention treatment was carried out. Although the lead screw pair has a dust ring, the cast iron dust is very small and easily adheres to the surface of the lead screw. If a small amount of dust enters the drive surface of the lead screw pair, the grinding effect of dust will exacerbate the wear of the lead screw pair, leading to a decline in lead screw accuracy and reduced service life.
导轨丝杠的原装配步骤及装配工艺问题相关内容就讲解到这里了,您对此有怎样的疑惑或者需求,就来我们网站http://www.jngongrun.com咨询吧!
The original assembly steps and assembly process of the guide rail lead screw are explained here. If you have any doubts or needs about this, please come to our website http://www.jngongrun.com Consult!
- 上一篇:精密滚珠丝杠轴向跳动严重超差的原因
- 下一篇:滚珠丝杠稳定性不够的表现
- 导轨防腐蚀措施有哪些...<>
- 滚珠丝杠的循环方式解...<>
- 导轨丝杆在陶瓷雕铣机...<>
- 导轨运行阻力怎么测量...<>
- 丝杠传动中的回差现象...<>
相关: